Loose
expansion factor
Compacted
expansion factor
Compaction
ratio
Compaction
percent
Stowage
factor
Compaction
percent
Chapter 7. Chips, Sawdust,
Planer Shavings, Bark, and Hog Fuel
|
Previous chapters have presented material
balances that can be used to estimate the fraction of a log recovered
in a residue form. There are many factors that affect chip and residue
measures and associated conversion factors. These include:
Size and geometry: The differences
in physical characteristics of these residues are obvious and affect
how they occupy a unit of space.
Specific gravity: Wood and bark
densities differ between species (Tables 1-1, 7-5).
Moisture content: Wood and bark
moisture contents vary between species (Table 1-1), and water may
be added during pond storage and debarking. Buyers and sellers of
residues and statistical reporting organizations generally devise
some method for correcting to the oven-dry state.
Degree of compaction: Over time,
chips and residues will settle due to gravity. Also, mechanical
and pneumatic compaction can be used to pack more residue into a
given space.
Quantities of chips and residues are measured in
units of volume or weight. This chapter discusses volumetric expansion
factors and bulk densities for these products, typical units of
measure and conversion, and residue yields, and also presents examples
that integrate this material.
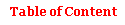
Expansion Factors, Relative Solid Volume,
and Compaction
To illustrate these terms, consider a log
containing 5 cubic feetof solid wood (Vsw) that is chipped. Obviously,
the chips will occupy more space than 5 cubic feet.
Expansion
(Fluffing) Factor
Loose Expansion Factor.
Immediately after chipping, suppose the loose chips occupy 15 cubic
feet (Vp). The expansion factor (E), also called the fluffing
factor, is
E (loose) = Vp / Vsw = 15 ft3
/ 5 ft3 = 3.00.
Note that when Vsw and Vp are measured in cubic
meters, the expansion factor has the same value.
Compacted Expansion
Factor. Loose chips will settle over time due to gravity,
or they may be physically compacted by equipment. Suppose the chips
are compacted so the space occupied (Vp) reduces to 12 cubic feet.
The expansion factor is
E (compacted) = 12 ft3
/ 5 ft3 = 2.40.
These calculations illustrate the importance of
noting the degree of compaction associated with a particular expansion
factor. Measures of compaction are discussed below.
Relative Solid Volume
The reciprocal of the expansion factor measures
the number of solid cubic feet (cubic meters) that will yield a
cubic foot (cubic meter) of residue. Continuing the example, relative
solid volume (RSV), also termed volume occupancy, is
RSV (loose) = 1 / E (loose)
= 1 / 3. 00 = 0.333.
RSV (compacted) = 1 / E (compacted)
= 1 / 2.40 = 0.417.
Some multiply RSV by 100 to express it as a percentage;
in this form it is sometimes called a compaction
rate.
Compaction
Compaction Ratio.
A common measure of compaction is the compaction ratio (CR),
which is
CR = Vp (loose) / Vp
(compacted)
= 15 ft3 /
12 ft3 = 1.25.
CR = E (loose) / E (compacted)
= 3.00 / 2.40 = 1.25.
CR can also be calculated from the relative solid volumes. It has a value of
one for loose residue and increases as the particles become more
compacted. A maximum value for CR can be estimated if it is assumed
that the maximum compaction possible would compress the residue
to the original volume of solid wood. Under these conditions:
Vp (compacted) = Vsw
hence
CR = 15 ft3 / 5 ft3 = 3.00.
In other words, the limiting value of the compaction
ratio is numerically equal to the expansion factor for loose particles.
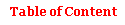
Compaction Percent.
A less common compaction value can be obtained from volume changes.
From the example, the maximum compaction from loose chips to solid
wood is 10 cubic feet, while the actual compaction is 3 cubic feet.
Actual compaction as a percentage of the maximum possible is
Compaction % = 100 * [Vp (loose) - Vp
(compacted)] / [Vp (loose) - Vsw]
= 100 * (15 - 12) / (15 - 5)
= 30%.
Summary
Table
7-1 presents expansion factors for various types of residues
and corresponding relative solid volumes. Also shown are conversions
from Imperial to metric and equivalents when residues are measured
in 200 cubic feet volumetric units (see p. 87). Tables 7-2 and
7-3 present additional sources of expansion factor and compaction
ratios. The conversion methods applied to the expansion factors
in Table 7-1 can also be applied to the expansion factors presented
in Table 7-2.
Bulk
Density
Bulk density (BD) refers to residue weight divided by residue volume.
Suppose the example log has a moisture content of 80% MCod
(44.4% MCw)and specific gravity (SGg)
is 0.48 (see Chapter 1 for definitions). Using methods presented
in Chapter 1, wood density is 53.9 wet pounds per green cubic
foot. This is composed of 29.9 lb of oven-dry wood plus 24.0 lb
of water. The term basic density
is sometimes used to refer to the oven-dry weight per cubic foot
(i.e., 29.9 lb/ft3). The chips
from the 5 cubic-foot log have the following weight distribution:
Condition
|
Weight (lb)
|
Percent
|
Oven-dry wood (Wod)
|
149.5
|
55.6
|
Water
(MCw)
|
120.0
|
44.4
|
Wood +
water (Wwet)
|
269.5
|
100.0
|
The term solids
fraction refers to the percentage of total weight that
is oven-dry wood.
As was described for solid wood density
in Chapter 1, bulk density can be calculated for any combination
of numerator (weight) and denominator (volume) moisture contents,
hence it is important to specify these conditions. The more common
cases are given in the remainder of this section.
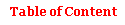
Oven-dry
Bulk Density
This is the oven-dry weight per green cubic foot
of residue. Divide the weight of oven-dry wood (Wod) by the residue volume (Vp)
BDod (loose) = Wod / Vp (loose)
= 149.5 lb / 15 ft3
= 10.0.
BDod (compacted) = Wod / Vp (compacted)
= 149.5 lb / 12 ft3
= 12.5.
The same results can also be obtained by dividing
the basic density (29.9 lb/ft3) by the appropriate expansion factor.
These bulk densities indicate the amount
of oven-dry wood present in each loose or compacted green
cubic foot of residue. They are important in residue
transactions because purchasers wish to pay only for wood and
therefore want the weight of water excluded. The residue volume
is green, since these are undried chips fresh from the log. In
cases where residues are dried or manufactured from dry wood,
these bulk densities would change because wood shrinkage will
modify the volume the residue occupies. This will be illustrated
below.
Wet Bulk Density
Bulk density can also be calculated with
the moisture content included in the weight (total weight per
green cubic foot of residue):
BDwet (loose) = Wwet / Vp (loose)
= (269.5 lb / 15 ft3)
= 18.0.
BDwet (compacted) = Wwet / Vp
(compacted) = (269.5 lb / 12 ft3)
= 22.5.
The same results can also be obtained by dividing
the wet wood density (53.9 lb/ft3) by the appropriate expansion factor. These values are useful
for estimating actual weights and loadings on equipment.
For the same compaction, knowledge of
moisture content allows conversion between BDod and
BDwet:
BDwet
= BDod * (1 + MCod
/ 100).
Effect of Drying (Shrinkage)on Bulk
Density
Bulk densities of dry residues or residues manufactured
from dry wood will differ from those in the preceding example.
One reason is that the type of residue may be different. Examples
are planer shavings and sander dust obtained when kiln-dried wood
is surfaced; these residue forms may have different expansion
factors. Another reason is that because wood shrinks as it dries,
the residue occupies less space. Since many secondary wood products
industries, such as millwork and furniture, utilize dry wood,
their oven-dry bulk densities will be higher and their wet bulk
densities will be lower due to the effects of shrinkage and lower
moisture content. See Example 1.
Summary
This section has demonstrated
how various factors affect bulk density calculations. Tables
7-2 and 7-3 present data illustrating the influence of mill
source (residue type) and species on bulk densities. It should
be obvious from the discussion that bulk density is ambiguous
without clear statement of the species (wood specific gravity),
type of residue, degree of compaction, and the moisture content
of both the numerator and denominator.
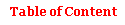
Units
of Residue Measure and Conversions
The
200 Cubic Foot Volumetric Unit
A unit representing 200 cubic feet of space is a very
common measure for residues. It is sometimes referred to as a
gravity packed unit (GPU). Care should be
taken when the word unit is used, since it may refer to other
measures (e.g., bone-dry unit in the next section).
Suppose 5 cubic feet
of solid green wood is dried to 10% MCod (9.1% MCw)
and that the species has SGg = 0.48 and 15%
total volumetric shrinkage.
As seen in Chapter 1, shrinkage reduces the volume
of solid wood to 4.5 cubic feet. If this dry wood is chipped with
the same equipment that converted the green log into 15 cubic
feetof green chips, the expansion factor of 3.00 predicts that
the loose dry chips will occupy 13.5 cubic feet. The same result
is obtained by applying volumetric shrinkage to the drying of
the green chips to 10% MCod.
If the dry chips are compacted to the same degree as the green
chips, the compacted volume is 10.8 cubic feet.
Using the methods explained in Chapter 1, we will
find the weight density of this dry wood to be 36.55 lb/ft3.
Of this, 33.2 pounds are oven-dry wood and 3.35 pounds are water.
The weight distribution of the dry chips is
Condition |
Weight (lb)
|
Percent
|
|
Oven-dry
wood (Wod) |
149.5
|
90.9
|
Water
(MCw) |
5.0
|
9.1
|
Wood
+ water (Wwet) |
164.5
|
100.0
|
Note that the solids fraction has risen to 90.9%.
Using the previously calculated expansion factor for loose chips,
bulk densities are
BDod
(loose) = 149.5 lb / 13.5 ft3 =
11.1.
BDwet (loose)
= 164.5 lb / 13.5 ft3 =
12.2.
Calculations for compacted chips are similar except
the compacted chip volume of 10.8 cubic feetis substituted. These
results can also be obtained by dividing "basic" and
wet wood densities by the loose expansion factor.
Note that the cubic foot volume here refers to
volume that remains after shrinkage to 10% MCod
rather than the original green volume. The difference between
the oven-dry and wet bulk densities has narrowed. The oven-dry
bulk density increased because the volume occupied by the dry
wood is less. The wet bulk density is also based on the smaller
volume occupancy, but this is offset by the great reduction in
weight of water. Hence the net effect is for the wet bulk density
to decrease.
The solid equivalent of a unit varies
depending on particle geometry and degree of compaction. Table
7-1, column 7, divides the expansion factors into 200 to estimate
the number of solid cubic feet of wood (or bark) that will expand
to fill a unit.
Table 7-3. Average moisture content (MCw)
and bulk density of various wood residues.
|
|
|
|
|
|
|
|
Green
|
|
Oven-dry
|
|
|
Residue
|
MCw
|
Mean SE
|
|
Mean
SE
|
|
|
|
U.S. South
|
|
|
|
|
Hardwood sawdust and bark
|
45
|
25.8
0.30 14.2 0.11
|
|
|
Mixed pine-hardwood sawdust
|
41
|
23.1
0.44 13.7 0.31
|
|
|
Clean hardwood pulp chips
|
43
|
22.9
0.55 13.1 0.58
|
|
|
Hardwood whole-tree chips
|
35
|
20.4
0.11 13.2 0.06
|
|
|
Pine whole-tree chips
|
40
|
18.8
0.10 11.3 0.08
|
|
|
Hogged dry trims (hardwood)
|
12
|
15.7
0.40 13.8 0.23
|
|
|
Shavings (hardwood)
|
8
|
10.8
0.59 9.8 0.55
|
|
|
|
|
|
|
|
Western
|
|
Oven-dry density (lb/ft3)
|
|
|
Hogged fuel
|
|
7.9 - 11.4
|
|
|
Sawdust
|
|
8.0 - 11.2
|
|
|
Bark
|
|
8.5 - 12.6
|
|
|
Secondary mill sawdust
|
|
8.8 - 14.0
|
|
|
Shavings
|
|
3.8
- 7.9
|
|
|
Sources: U.S. South: Harris and Phillips
(1989). Western: Risbrut and Ellis (1981).
Column 9 presents reciprocals of column 7 (i.e.,
number of units that will result when one solid cubic foot is
converted into the corresponding residue type). Column 8 presents
the metric counterpart to column 7 (i.e., the number of solid
cubic meters that will expand to fill a cubic meter of space with
the particular residue).
Conversions:
1 unit = 200 ft = 5.66 m3.
1 m3 = 35.315 ft3
= 0.177 unit.
Weight
Measures
The common weight measures and conversions used in transactions
and in various statistical sources are shown in Table 7-4. The
weight of a bone-dry unit (BDU) was obtained by experimentally
weighing a number of cords of Douglas-fir slab wood that were
dried to 3 to 7% moisture content. The average weight, nearly
2,400 pounds, has become a standard basis for measuring residues.
Of these weight measures, the long ton
is the least common but is found in some statistical reports.
Due to moisture content variation, weights are generally corrected
to a zero percent moisture content (oven-dry or bone-dry). Consequently,
actual shipping weight will be much greater. Two useful conversions
are (Appendix 1, Table 2):
To convert lb/ft3 to kg/m3 multiply by 16.0185.
To convert
kg/m to lb/ft3 multiply by 0.062428.
Table 7-4. Residue weight measures and conversions.
|
|
|
|
|
|
Short
|
Long
|
|
|
|
|
|
Oven-dry
(lb)
|
Oven-dry
(kg)
|
ton
|
ton
|
BDU
|
Tonne
|
|
|
|
Short ton
|
2,000
|
907.18
|
1.000
|
0.909
|
0.833
|
0.907
|
|
|
Long ton
|
2,200
|
998.18
|
1.100
|
1.000
|
0.917
|
0.998
|
|
|
BDU
|
2,400
|
1,088.62
|
1.200
|
1.091
|
1.000
|
1.089
|
|
|
Tonne
|
2,204.62
|
1,000.0
|
1.102
|
1.002
|
0.919
|
1.000
|
|
|
|
|
|
|
|
|
|
|
|
|
Source: Calculated
by the author.
Stowage
Factor and Compaction in Shipping
Since wood chips and residues
are light in weight, compaction is very important to minimize
the transporation cost per ton.
Stowage Factor.
This is a marine term that measures the cubic volume of cargo
space for products of known weights. It represents the number
of cubic feet required, including void space, to contain a
long ton of a product. Therefore, a stowage factor
of 120 means that 120 cubic feet of space is needed to stow a
long ton of a particular product.
Compaction Percent.
Because of variability in moisture content, stowage factors for
chips are not reliable and an alternative, compaction percent,
is more commonly used. Compaction means the packing of chips so
the voids are minimized. The pulp and paper industry defines compaction
as the number of bone-dry units (BDU) that can be placed in a
200 cubic foot space. Thus one faces the potentially confusing
situation relating BDU (a weight measure) to GPU (a volume measure).
Compaction is usually expressed as a percentage.
A 100% compaction means that a BDU occupies exactly 200 cubic
feet, which implies a bulk density of 2,400 lb/200 ft3
= 12 lb/ft3. Similarly, 90% compaction
means that 0.90 BDU occupies 200 cubic feet (bulk density =
10.8 lb/ft3). With modern shiploading equipment, compaction percentages
of 100% or more are commonly achieved.
Compaction percent can be calculated by one of
the following formulas.
Compaction percent
= 100 * BDU * 200 / ship volume, ft3
= (long tons loaded) * 1.12 (100 - MCw)
* 200 / (1.2 * ship volume, ft3)
= 2,240 * 200 * (100 - MCw)
/
(stowage factor * 2,400)
= 186.6 (100 - MCw)
/ stowage factor.
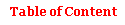
Residue
Yield
Sawdust
The volume of sawdust produced
in manufacturing lumber depends on sawkerf thickness, product
line (number of saw cut lines), and log diameter. For a given
log size and sawkerf, a mill producing smaller lumber items will
generate more sawdust than a mill cutting large timbers. The material
balance references in Chapter 4 are a good source of average sawdust
yields in solid wood equivalent. The sawdust expansion factor
in Table 7-1 or 7-2
should be applied to convert these solid wood equivalents to volume
of sawdust as shipped.
Pulp Chips
Pulp chips are obtained from three
principal sources: (1) whole logs, (2) sawmill slabs, edgings,
and trimmings, and (3) veneer mill scraps and peeler cores, if
the latter are not sold to stud sawmills or preservative plants
for posts. The material balances in Chapters 4 and 5 provide estimates
of average chip yields in solid wood equivalent from these processes.
The chip expansion factor in Table
7-1 or 7-2 should
be applied to convert these solid wood equivalents to volume of
chips as shipped. The material balances assume that residues recovered
as chips are fully utilized by pulp mills. Actually, a reject
loss on the order of 2 to 5% will occur during pulp chip screening.
This reject loss will be at the upper or lower end of this range
depending on the condition of the chipper, the chip specification,
and whether oversize chips are rechipped.
Planer Shavings
The volume of planer shavings
obtained depends on the fraction of lumber output that is planed
and the difference between the rough and surfaced dimensions.
The material balances and computational methods in Chapter 4 can
be used to estimate average shaving yields. Since these material
balance estimates are in solid wood form, the expansion factor
in Table 7-1 or 7-2
must be applied to get volume as shipped.
Bark
Bark volume varies with species,
position on the tree, and tree size. Average bark volume can be
estimated either as a percent of total volume (including bark)
or as a percent of wood volume:
Bark volume as a percent of total volume
(BTV%) = (dob2 - dib2)
/ dob2 * 100
Bark volume as a percent of wood volume
(BWV%) = (dob2 - dib2
) / dib2 * 100
where dob = diameter outside bark
dib = diameter inside
bark.
For example, for a log measuring 20 inches in diameter inside bark,
with bark one inch thick, the bark percentages are
BTV% = (222
- 202) / 222
* 100 = 17.4%.
BWV% = (222
- 202) / 202
* 100 = 21.0%.
This calculation is likely to overestimate
the true bark volume because of fissures and voids in the bark.
A range of 26 to 28% void volume was found for three softwood
species (Krier and River 1968), hence the above results should
be reduced by this amount. The recovered bark may be lower, due
to miscellaneous losses during harvesting, log handling, and debarking.
Smith and Kozak (1967) developed bark
thickness regressions for a variety of western Canadian species.
Table 7-5 presents average total bark volume percentages, moisture
contents, and specific gravities of inner and outer bark. The
bark moisture contents reflect conditions that would normally
be found in logs and do not include additional water from pond
storage or water added during debarking.
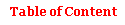
Table
7-5. Bark contents of western species.
|
|
|
|
|
|
Bark
volume,
|
% of
|
% of
|
|
|
percent
of
|
total
|
total
|
|
Species
|
Wood Total
|
bark MCod% SGg
|
bark MCod% SGg
|
|
|
SOFTWOODS
|
|
|
|
|
|
|
|
|
|
Cedar
|
|
|
|
|
Western redcedar
|
16
14
|
36 88 0.36
|
64
37 0.38
|
|
Yellow (Alaska)
|
15
13
|
52
145 0.41
|
48
79 0.38
|
|
|
|
|
|
|
Douglas-fir
|
28
22
|
38
133 0.45
|
62
80 0.43
|
|
|
|
|
|
|
Fir, true
|
13
12
|
65
77 0.52
|
35
40 0.58
|
|
|
|
|
|
|
Hemlock, western
|
20
16
|
54
134 0.45
|
46
65 0.56
|
|
|
|
|
|
|
Pine
|
|
|
|
|
Lodgepole
|
11
10
|
30
128 0.34
|
70
42 0.51
|
|
Ponderosa
|
31
24
|
12
78 0.36
|
88
21 0.34
|
|
Western white
|
13
12
|
23
118 0.31
|
77
75 0.54
|
|
|
|
|
|
|
Spruce
|
|
|
|
|
Engelmann
|
15
13
|
59
121 0.45
|
41
60 0.53
|
|
Sitka
|
9
9
|
45
112 0.44
|
55
55 0.62
|
|
|
|
|
|
|
Hardwoods
|
|
|
|
|
|
|
|
|
|
Red alder
|
16
14
|
56
88 0.52
|
44
66 0.62
|
|
Aspen
|
20
17
|
35
121 0.37
|
65
93 0.54
|
|
Birch
|
22
18
|
65
68 0.63
|
35
22 0.66
|
|
Black cottonwood
|
12
11
|
48
130 0.41
|
52
77 0.44
|
|
Bigleaf maple
|
19 16
|
68 134 0.66
|
32 70
0.45
|
|
|
Source: Smith
and Kozak (1971).
Hog Fuel
Hog fuel is generally a mix of
bark, sawdust, and planer shavings. The relative amount of each
depends on a particular mill's marketing alternatives for these
residues. The mix can be estimated as a weighted average using
the information presented in the appropriate yield sections (see
Estimating a Hog Fuel Mix below). If an estimate is needed with
a high degree of confidence, samples of the hog fuel in question
should be analyzed.
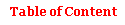
Residue
Calculation Examples
Estimating Yield from Plywood
The following procedure can be used for
lumber, veneer, plywood, and so forth. Assume that it is desired
to estimate the number of 200 cubic foot units of chips recovered
per 1,000 square feet (3/8 inch basis) of Douglas-fir plywood.
The average mill-length block is 15 inches in diameter.
1. From the plywood material balance studies
(Fahey and Willits 1991), about 25% of a mill-length veneer block
is recovered as chippable residue, and about 50% is recovered
as dry veneer. About 12% of the dry veneer will be lost in making
plywood, so about 45% of the block will be plywood.
2. Chapter 5 shows that 1,000 square feet,
3/8 inch basis, plywood has a cubic volume of 31.25 cubic feet.
3. Since the cubic volume of plywood (31.25
ft3) represents 45% of the cubic
block volume and since the cubic volume of clean chips represents
25% of the block volume, the solid wood equivalent volume of
chips can be estimated by proportions as follows:
45 / 31.25 = 25 / x.
Solving, yields x
= 17.4 ft3 solid equivalent of
chips recovered per 1,000 ft2,
3/8 inch, plywood.
4. Convert the solid chip volume by the
compacted chip expansion factor of Table
7-1. Compacted chips
= 17.4 ft3 solid chips * 2.50 ft3compact
chips per solid ft3 = 43.5 ft3.
5. Since a unit is 200 cubic feet, there
are 43.5 / 200 = 0.218 units of compact chips recovered per
1,000 square feet of 3/8 inch basis plywood.
Estimating Yield per Cunit
of Log Input
Assume a plywood process with the same
conditions as indicated above.
1. From the material balance equations (Fahey
and Willits 1991), about 25% of a mill-length veneer block is
recovered as chippable residue.
2. Yield of chips = 100 ft3/cunit * 0.25 = 25 ft3
solid chips.
3. Multiply by the compacted chip expansion
factor in Table 7-1. Compacted
chips = 25 ft3solid chips *
2.50 ft3 compact chips per ft3 solid chips = 62.5 ft3.
4. Therefore, a cunit of veneer blocks
yields 62.5 / 200 = 0.3125 units of compact chips.
Converting Units of Residue
to Weight
How many units of pulp chips equal an
oven-dry short ton?
1. Assume the species is Douglas-fir, which
has a SGg of 0.45 (Table 1-1).
Table 1-2 shows the weight density at 0% MCod,
or 28.1 pounds per solid cubic foot.
2. Divide by the compact chip expansion
factor (Table 7-1) to get
a bulk density of 11.24 oven-dry lb/ft3 compact chips. Alternatively, use a bulk density based on
samples.
3. Divide 2,000 pounds in a short ton by
the bulk density estimate to get the number of cubic feet of compacted
chips per short ton: 2,000 / 11.24 = 178 ft3.
4. Since a unit is 200 cubic feet, a short
ton represents 178 / 200 = 0.89 units under these conditions.
Note:
Simple division shows that for a 200 cubic foot unit to exactly
equal a short ton, the bulk density would be 2,000 / 200 = 10
oven-dry lb/ft3 residue. Similar
calculations for other weight measures imply oven-dry bulk densities
as follows:
Long ton 11.00
BDU
12.00
Tonne
11.02.
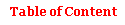
Estimating a Hog Fuel Mix
Assume that the hog fuel for a cunit
of Douglas-fir logs processed in a sawmill will contain all of
the sawdust, planer shavings, and bark produced by the mill.
1. From the material balances in Chapter
4 and the bark section in this chapter, assume the following
recoveries as percentages of green wood volume: sawdust, 8%; shavings,
5%; bark, 28%. Reduce the bark fraction by 30% to account for
fissures, voids, and processing losses so that the net bark fraction
is 20%.
2. Column 1 of the table below multiplies
these recovery percents by the 100 cubic feet in a cunit to give
solid volume yields in cubic feet.
3. Column 2 lists the appropriate residue
expan-sion factors from Table
7-1, and column 3 is the expanded residue volume in cubic
feet after multiplying column 1 by column 2.
4. Columns 4 and 5 present MCod
and SGg assumptions. It
is assumed that sawdust is generated when processing green wood
with an MCod of 80%. The planer shavings are assumed to be generated
after kiln drying to an average MCod of 16%. The bark MCod and SGg are weighted averages of inner and outer bark of Douglas-fir
from Table 7-5. Columns 6 and 7 are estimates of wet and oven-dry
solid wood densities using Table 1-2.
5. Dividing the solid wood densities of
columns 6 and 7 by the expansion factors in column 2 results in
residue green and dry bulk densities in columns 8 and 9.
6. Multiplying the residue volume in column
3 by the green and dry bulk densities in columns 8 and 9 results
in green and dry residue weights in columns 10 and 11.
7. Totals of columns 3, 10, and 11 give
the final hog fuel values of interest.
For the conditions assumed here, a cunit of logs
yields 92 cubic feet (0.46 unit) of hog fuel having a green weight
of 1,767 pounds (green bulk density of 19.2 lb/ft3) and oven-dry weight of 972 pounds (dry bulk density of
10.6 lb/ft3). The hog fuel is equal
to 0.40 BDU.
Residue
|
(1)
|
(2)
|
(3)
|
(4)
|
(5)
|
(6)
|
(7)
|
(8)
|
(9)
|
(10)
|
(11)
|
Sawdust
|
10
|
2.50
|
25
|
80
|
0.45
|
50.6
|
28.1
|
20.2
|
11.2
|
506
|
281
|
Shaving
|
5
|
4.00
|
20
|
16
|
0.45
|
32.6
|
28.1
|
8.2
|
7.0
|
163
|
141
|
Bark
|
20
|
2.35
|
47
|
100
|
0.44
|
54.9
|
27.5
|
23.4
|
11.7
|
1,098
|
550
|
|
Total
|
|
|
92
|
|
|
|
|
|
|
1,767
|
972
|
|